Hydroxypropyl methylcellulose (HPMC) and methyl hydroxyethyl cellulose (MHEC) are both crucial compounds in the construction and pharmaceutical industries, primarily known for their roles as thickeners, binders, and emulsifiers. Despite their similar appearances and overlapping functions, distinct chemical compositions and properties set them apart, leading to their unique applications.
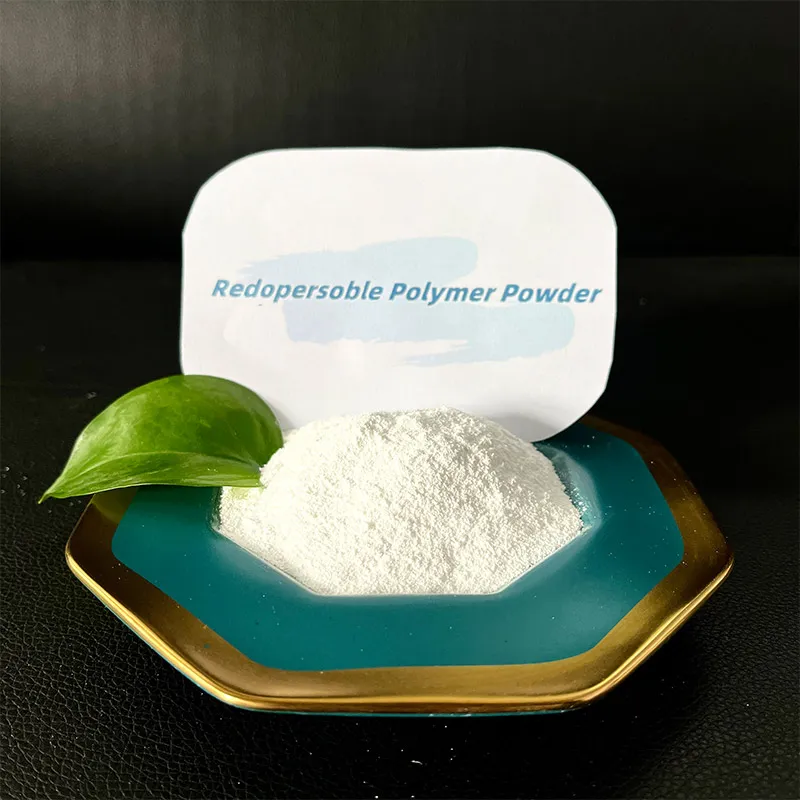
HPMC is a nonionic cellulose ether derived from the chemical modification of cellulose through methyl and hydroxypropyl groups. This modification lends HPMC several distinct properties, such as high water retention, film formation, and thermal gelation abilities. These characteristics make it indispensable in the construction industry, particularly in tile adhesives, cement renders, and gypsum products. Its ability to retain moisture is crucial in preventing cracking and improving workability during construction applications. Moreover, HPMC's bio-compatibility and non-toxic nature make it highly suitable for pharmaceutical applications, including drug delivery systems for controlled release, where precise administration of medication is paramount.
On the other hand, MHEC, which boasts modifications with methyl and hydroxyethyl groups instead, has been designed to exhibit a high level of solubility in cold water and improved workability in formulations. This makes it particularly valuable for applications requiring excellent water retention and slip resistance, such as in the formulation of cement-based mortars. MHEC effectively enhances adhesion and open time, essential in ensuring superior bonding and satisfactory application of paints and coatings. Additionally, its ease of dissolution in both hot and cold water grants it versatility and adaptability across an array of conditions.
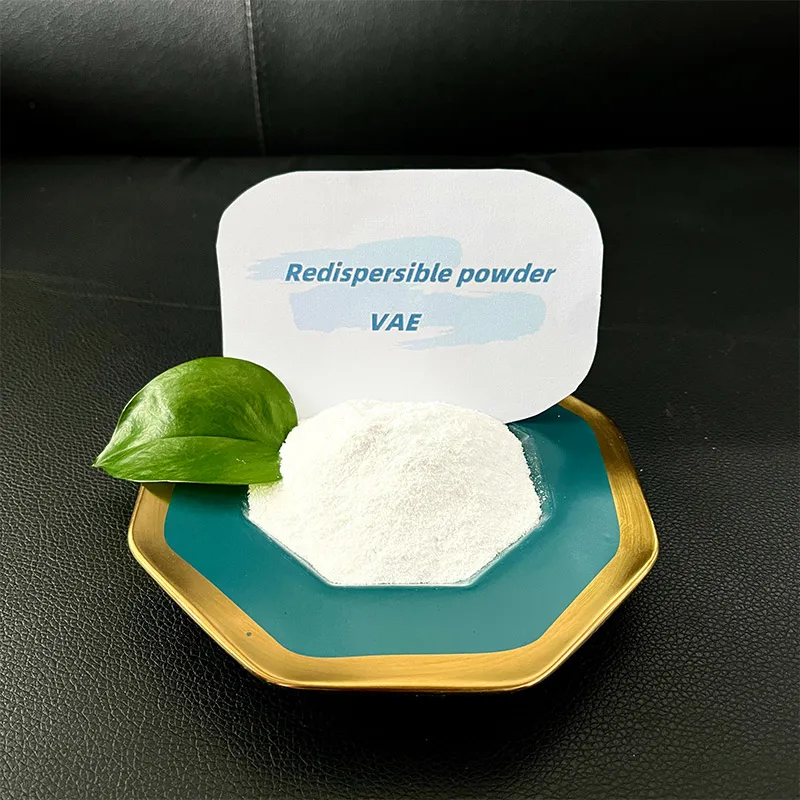
When comparing HPMC and MHEC, it's essential to highlight their distinctive thermal gelation properties. HPMC exhibits a more clearly defined gel point temperature, making it advantageous for products requiring stability under varied temperature conditions. This characteristic is particularly pivotal in construction settings where temperature fluctuations can significantly impact material performance. MHEC, while also possessing thermal gelation capabilities, delivers slightly different responses to temperature changes, which can be selected based on specific application needs.
difference between hpmc and mhec
Sustainability and safety are ever-increasing concerns in contemporary industrial practices. Both HPMC and MHEC align well with these values, as they are derived from natural cellulose and are biodegradable. However, HPMC is often preferred in the pharmaceutical sector due to its long-standing safety profile and extensive research supporting its use in consumable products. MHEC, while also safe, does not boast the same depth of usage history in the pharmaceutical industry, which may influence its selection for certain drug formulations.
Application cost is another factor distinguishing HPMC from MHEC. While both cellulose ethers are similarly priced, slight variations can occur based on supply chain dynamics and regional availability. Generally,
the choice between these two compounds will hinge on the specific functional requirements of the application rather than economic differences. Decision-makers in industries where precise formulations are critical should conduct rigorous testing to determine which compound best meets their needs.
In conclusion, while both HPMC and MHEC serve as valuable assets in numerous industrial applications, careful consideration of their unique properties and specific application requirements is imperative. The differences in solubility, thermal behavior, and historical usage suggest that neither is inherently superior but rather suited to different scenarios. By leveraging the precise attributes of each cellulose ether, companies can optimize their formulations for improved performance and cost-effectiveness. Understanding these nuances not only enhances manufacturing processes but also aligns product development with evolving industry standards and sustainability goals.