Polypropylene fiber reinforced concrete (PFRC) represents a cutting-edge advancement in the field of construction materials, known for its combination of high-performance features and cost-effective application. As the construction industry continually seeks sustainable and innovative solutions, PFRC stands out due to its enhanced durability, crack resistance, and overall structural integrity. This article delves into the intricacies of PFRC mix design and its unparalleled advantages for construction projects.
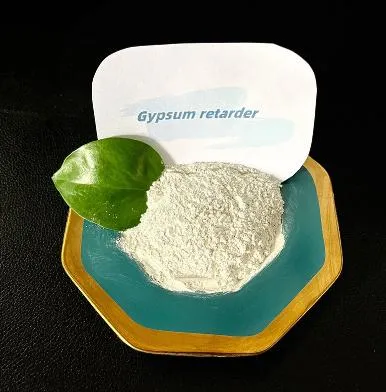
The essence of PFRC lies in the integration of fine polypropylene fibers within the concrete matrix. These fibers, typically ranging from 12 to 50mm in length and possessing diameters of around 15-50 μm, act as secondary reinforcement. They complement the traditional steel reinforcement processes, offering a multidimensional approach to minimizing micro-cracks. The primary benefit is the significant reduction in crack propagation, particularly during the plastic and hardening phases of the concrete, thereby enhancing the lifespan of the structure.
Central to the success of PFRC is an optimal mix design that is fine-tuned to achieve the desired mechanical properties. A typical mix requires careful consideration of the following components cement, aggregates (fine and coarse), water, chemical admixtures, and polypropylene fibers. The proportioning of these materials is crucial to achieving a balance between workability, strength, and durability. It's essential to perform trial mixes and adjustments based on the specific application and the environmental conditions of the site.
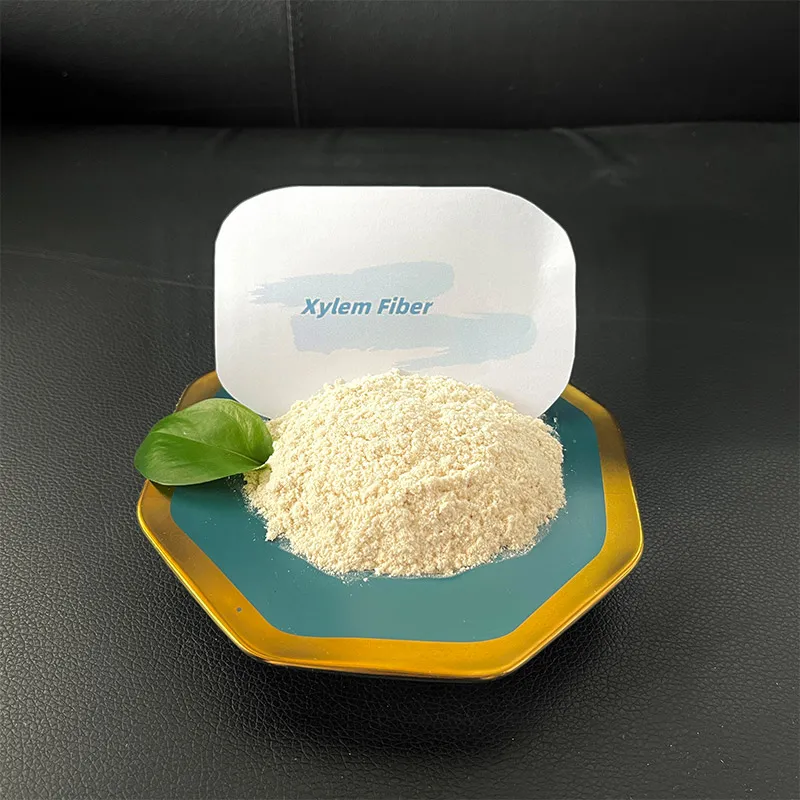
For an effective PFRC mix, start by selecting a high-quality Portland cement to ensure binding strength. Aggregates should be clean, free from deleterious materials, and well-graded to achieve optimal compaction and reduce void content. Water-to-cement (w/c) ratio is a critical factor; a lower w/c ratio generally improves strength and reduces permeability, which is crucial for maintaining the effectiveness of the fibers. Admixtures such as plasticizers and superplasticizers can be added to enhance workability without increasing the w/c ratio, which is particularly important for high-fiber volume mixes.
Incorporating polypropylene fibers requires precise dosing and even distribution throughout the mix. Typically, fiber content ranges from 0.1% to 0.3% by volume, depending on the desired level of reinforcement. During the mixing process, gradual addition of fibers into the concrete mix avoids clumping and ensures uniform dispersion. Achieving this homogeneity is vital for the fibers to effectively combat shrinkage and cracking.
mix design of polypropylene fiber reinforced concrete
When assessing PFRC for a project, its performance benefits extend beyond mere functional attributes. PFRC enhances the overall toughness of the concrete, absorbing energy and resisting dynamic impacts that may occur due to seismic activities or harsh weather conditions. Its durability is particularly notable in environments exposed to chloride or sulfate attacks, common in coastal and industrial regions. The fibers act as a barrier, inhibiting the ingress of deleterious agents that can compromise structural integrity.
Furthermore, PFRC is lauded for its sustainability. The use of polypropylene fibers reduces the dependence on traditional reinforcement, which is not only resource-intensive but also has a higher carbon footprint. By integrating fibers, structures can achieve similar, if not superior, strength and durability with less material use and environmental impact. This aligns with modern building trends emphasizing green construction practices.
Given the complexity and specialized nature of PFRC, consulting experienced professionals in concrete technology is advised for any project planning to utilize this material. Engineers and architects with a profound understanding of fibrous materials can provide invaluable guidance in mix design optimization, ensuring the structural goals are met without compromising on cost or efficiency.
With an increasing number of successful projects globally, PFRC continues to gain credibility and trust within the industry. Its proven track record in various applications, from pavements and bridges to industrial floors and precast elements, highlights its versatility and reliability as a construction material of choice.
In conclusion, polypropylene fiber reinforced concrete offers a remarkable combination of enhanced structural properties, sustainability, and cost-efficiency. Its strategic use in construction not only furthers the longevity and performance of concrete structures but also adheres to stringent environmental and engineering standards. As the industry advances, PFRC primes itself as a forerunner in innovative construction solutions, backed by a foundation of expertise and authoritative research.