The process of manufacturing Hydroxypropyl Methylcellulose (HPMC) is both intricate and fascinating, reflecting the harmonious blend of chemistry and industrial engineering. As a seasoned SEO expert, I aim to shed light on this subject, ensuring not only higher visibility but also an authoritative presence online, particularly in the eyes of Google.
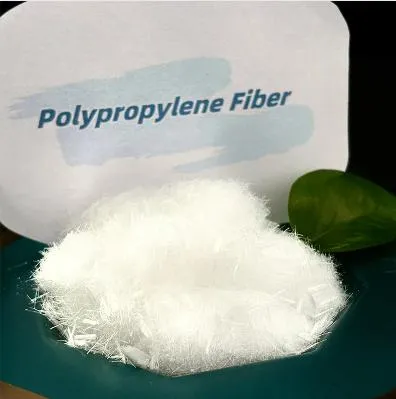
HPMC, an essential derivative of cellulose, is fundamental in various industries due to its versatile properties. These include its thickening, emulsifying, and binding abilities, making it a key ingredient in sectors ranging from pharmaceuticals to construction.
Manufacturing HPMC begins with selecting high-quality cellulose, generally sourced from wood pulp or cotton linters. The purity of the cellulose source is paramount, as it directly impacts the efficacy and quality of the final product. The cellulose undergoes a series of purification steps to ensure the absence of impurities, preparing it for the crucial chemical transformation phase.
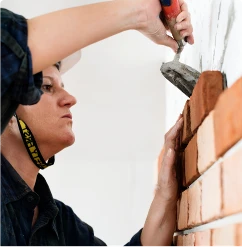
The next step is the etherification process. Here, cellulose reacts with reactive alkylene oxides, typically propylene oxide and methyl chloride, under controlled alkaline conditions. This step introduces the hydroxypropyl and methyl groups into the cellulose chain. The degree of substitution and the distribution of hydroxypropyl and methyl groups can be meticulously controlled by adjusting reaction conditions, thus tailoring the HPMC to specific application requirements. This customization is pivotal for its application-specific functionality, such as viscosity or dissolution rates.
Temperature and pressure regulation during the reaction are critical factors influencing the uniformity and quality of the resultant HPMC. Advanced manufacturing setups employ real-time monitoring systems to ensure optimal reaction conditions and minimize any potential deviations that could affect product quality.
Post-etherification, the reaction mixture undergoes a series of meticulous washing and filtration stages. These steps are designed to remove by-products, unreacted chemicals, and any excess alkali. The purification process is critical as it directly affects the safety and performance of HPMC in its end-use industries.
hpmc manufacturing process
Following purification, the material is then dried thoroughly. Drying is a crucial step because HPMC’s hygroscopic nature could lead to undesired moisture absorption if not handled correctly. Modern manufacturing environments use efficient drying technologies such as fluidized bed dryers, ensuring uniform moisture content in the final product. This is particularly important for applications requiring a precise viscosity specification.
The dried HPMC is then milled into a fine powder, enhancing its solubility and dispersibility properties. Particle size distribution is closely monitored during this phase, with different specifications provided depending on the intended application. Whether it's for a fast-setting concrete admixture or a slow-dissolving pharmaceutical binder, the particle size plays a significant role in its performance.
Quality control is a continuous theme throughout HPMC manufacturing. State-of-the-art laboratories conduct rigorous testing protocols, assessing parameters such as viscosity, purity, and moisture content. These tests ensure that the HPMC meets stringent industry standards, further reinforcing the trust and dependability users associate with top-tier suppliers.
The environmental impact of HPMC production is also mitigated through the implementation of eco-friendly practices. Recycling solvents and optimizing energy usage are examples of how the industry strives to balance economic vitality with environmental stewardship.
Harnessing decades of expertise, manufacturers continually refine their processes to enhance the performance characteristics and sustainable production of HPMC. As industries evolve, so too do the functionalities demanded of HPMC, spurring ongoing research and development efforts.
In conclusion, the manufacturing process of HPMC epitomizes the fusion of expert knowledge and cutting-edge technology. Its complexity warrants a deep understanding of chemical processes, mechanical systems, and quality assurance measures, making it a captivating subject for those involved in its production or application. Sharing this process with clarity not only helps in reaching a wider audience but also establishes a foundation of trust and authority within the market and among potential users.